Can Industry 4.0 Bring 6th Sense to Inspection Activity?
Oh Really?
Human ability to see when something is failing has become better through non-destructive evaluation methods. It has evolved from highlighting surface to looking inside and now getting to point, where data analytics from diverse sources could provide a digital indication of damage that is yet to appear on the physical structure, kind of a sixth sense!
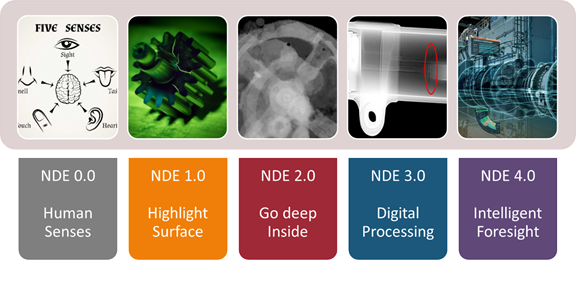
The Revolutions in Non-destructive Evaluation (NDE)
For centuries humans have taken care of their safety using the five basic senses – touch, sight, hearing, smell, and taste. The revolutions in manufacturing, infrastructure, and transportation systems came with unfortunate incidents and fatal accidents. The engineering community rose to the challenge of quality, safety, and reliability through non-destructive inspections. This important domain serving so many industries, has also seen its share of revolutions, aligned with the changing needs of the industrial revolutions, and enabled by similar suite of technologies.
The first inspection revolution was around highlighting the surface for human organic sensory perceptions. Tools such as lenses, colors or stethoscopes improved the detection capabilities of naked eye and human ear. Procedures made the outcome of the inspection comparable over time.
The second revolution in NDE used physical understanding of material response to electromagnetic or acoustic waves, which lie outside the range of human perception, into signals that can be interpreted by humans. This resulted in a “look inside” into the components or a better visualization of material inhomogeneities behind or close to the surface. For example – X-ray, gamma testing, ultrasonic, Infrared and terahertz detection, eddy current, etc.
The third revolution in NDE came along with computers and digitalization that simplified imaging and analysis of signals, such as X‑ray detectors, digital ultrasonic and eddy current equipment, and digital cameras. Robotics automated the processes, making them convenient, fast, and repeatable. The digital technologies offered another leap in managing inspection workflow data from acquisition, storage, processing, 2D and 3D imaging, interpretation, to communication. Data processing and sharing became the norm, and data security and integrity came in as a new challenge.
The fourth revolution in NDE (now) integrates the digital techniques (from the third) and physical methods of interrogating materials (from the second) in a closed loop manner transforming human intervention and enhancing inspection performance. Within the context of the physical-digital-physical loop of NDE 4.0; digital technologies and physical methods may continue to evolve independently, interdependently, or concurrently. The real value is in concurrent design of an inspection through application of Digital Twins and Digital Threads. This provides the ability to capture and leverage data right from materials and manufacturing processes to usage and in-service maintenance. The data captured across multiple assets, can be used to optimize predictive and prescriptive maintenance, repairs, and overhauls over the lifetime of an asset. The relevant data can be fed back to OEM for design improvements. NDE 4.0 also serves the emerging trends in custom manufacturing. Remote NDE can keep the inspector away from harm’s way and integration by “tele-presence” can bring additional specialists in the decision process from anywhere in the world quickly and affordably.
The role of human is changing from ‘human-in-the-loop’ to ‘human-on-the-loop’ from ‘human-outside-the-loop.’
Game Changer – Intelligent Inspection System
The continuous improvement in inspection capability is driven by the need and desire to pick smaller and smaller damage or material discontinuity (Crack, corrosion, delamination, foreign object inclusions) with higher and higher likelihood. It is called probability of detection (POD), typically characterized by an S-shaped curve. Just like with naked eye, we all have slightly different probability of seeing small stuff on the floor. Most of the time a small shiny spec on the kitchen tile floor could go unnoticed, however it is different, if you knew that your child broke a glass yesterday. You will likely scan a larger area looking for more such pieces. That is the power of knowledge, experience, and intelligence.
The Industry 4.0 can bring the ability to synthesis all of the data right from manufacturing, usage, environment, (digital history acting like a lifelong blackbox) and combine it with data from detected damage in other older assets (experience), the intelligent inspection system could predict with a certain probability that there is a discontinuity hiding here smaller than equipment’s ability to detect.
We have seen such capability in many domains. Ten years ago, Target store figured out a teen girl was pregnant before her father did (Forbes Feb 16, 2012). Amazon regularly ships products to the distribution centers nearest to your house based on your shopping patterns to cut down delivery time. Law enforcement agencies can thwart threats from social media chatter. That is the power of the data and intelligence augmentation.
The probability of detection by cyber-physical system using digitalized history can get better than intrinsic capability of the physical equipment, in a sense the 6th sense of the machine. Machine can predict with certain confidence that there is a signal here hidden in the noise, from an anomaly that will be detectable sometime in the near future.
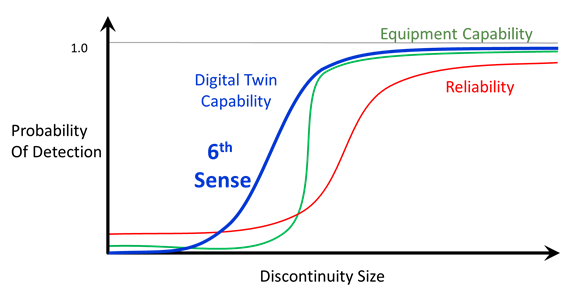
In Summary,
The NDE 2.0 changed the game providing inspectors with equipment to see hidden damage using physical waves.
The NDE 4.0 could change the game again by augmenting an inspector with an intelligent system to foresee a damage on the digital twin before the inspection equipment can pick it up on physical structure.
If you like this blog post, you will like our upcoming book “Welcome to the World of NDE 4.0” DM me or Johannes Vrana and we can alert you when it is available on Amazon.
For a dedicated session for your company, please reach out to Ripi Singh directly.