What Might be the Next Revolution?
Oh Really?
We have defined the digital-physical integration as Industry 4.0. We have seen advances in digital-biological systems and also the biological-physical systems. Is it time for Digital-Physical-Biological confluence to create a whole new world?
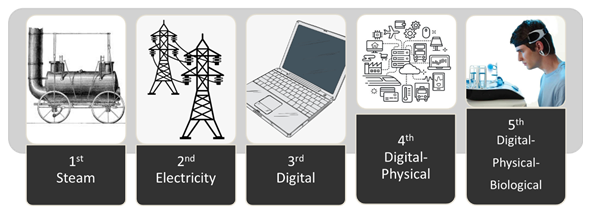
The Four Industrial Revolutions
Over the last three centuries, humanity has seen significant change in lifestyle, driven by three industrial revolutions. Currently, we are going through the fourth revolution. Briefly
The first industrial revolution brought a change from handcrafted forms of production to the mechanization of production with steam engines or regenerative energy sources such as water.
The second industrial revolution triggered by electric power, enabled new industries and mechanical production engineering. We mastered the control of physical materials and products.
The third industrial revolution came from development of computers, which allowed automated control of industrial production and revolutionized data processing. We mastered the digital space.
In the fourth industrial revolution, we are beginning to harness the potential of digital physical integration. A good example of the digital physical integration is a self-driving car. The car gathers the data from multiple cameras and sensors to determine its position, velocity, and separation to other cars. It uses the data in real time to take physical actions with an intent to reach the destination without collision or discomfort. A similar change is happening in industrial manufacturing and maintenance. In addition, there is a growing desire to make these cyber-physical systems learn from experience, adopt to variation in inputs, make select decisions, and act autonomously to accomplish an objective.
The Next Revolution
This is another form of confluence that has been emerging slowly but steadily. For many decades we have seen significant advancement in physical-biological systems such as prostheses and implants – artificial substitutes for body parts, nanomaterials, nanobiotechnology, biosensors, and bionics.
There is a serious research effort in the field of digital-biological systems such as Biocomputers which use biologically derived molecules, such as DNA and proteins, to perform digital or real computations. And now we are advancing the technologies to 3D printing of skin and organs.
Bringing Biology into the digital-physical systems of the fourth industrial revolution could usher in a next revolution – governed by digital-physical-biological confluence for purpose. We just do not know what that would look like. But we have some early indications of various use cases.
Intelligent Implants[1] is at the forefront of electrotherapeutic devices to treat disease and aid recovery in bone and other tissues. They pioneer the use of data, engineering, and biologics to bring novel, active and connected medical devices to healthcare. Their integrated devices facilitate treatment for the patient, as well as decision making for the healthcare professional.
A quadriplegic racer Rodrigo Hübner Mendes[2] was the first person ever to drive an F1 car using a sensor studded cap over his head that could pick up his brain activity to drive the car, in 2017.
Neuralink[3] is pushing the boundaries of innovation in neural engineering. They are designing the first neural implant that will let you control a computer or mobile device anywhere you go.
Global Human Body Models Consortium[4] (GHBMC) of seven automakers and one supplier have been consolidating their individual research and development activities in human body modeling into a single global effort to advance crash safety technology since 2006. These computers models have significant derivative applications in sports, aerospace, healthcare, wearables, forensics, and military as posted on social media by the author[5] in 2016. A private company Elemance[6] continues to develop and serve this applied innovation in form of proven, validated, finite element human body models, ready for simulation environments.
A combination of human body digital twin, understanding of genetics, and opportunity to 3D print organs opens serious opportunities in longevity, quality of life, and questions around ethics, hard to answer at this stage.
In Summary,
In some sense all sorts of combination of human-machine integration are on the horizon, not just artificial limbs and biocomputers. That would be an era of cyber-physical-biological confluence. And it could be very revolutionary.
Will his be the next revolution? what do you think?
If you like this blog post, you will like our monthly conversations on Innovation. You are invited to join by registering at www.inspiringnext.com/events
For a dedicated session for your company, please reach out to Ripi Singh directly.
[1] https://www.cipherbio.com/data-viz/organization/Intelligent%2BImplants
[2] EMOTIV x Rodrigo Hubner Mendes – Driving F1 car just by thinking, Aug 18, 2017. https://www.youtube.com/watch?v=NhmXaeaHkDc
[5] CAE in Bio-Mechanics – Imagine Next? Ripi Singh, May 4, 2016, https://www.linkedin.com/pulse/cae-bio-mechanics-imagine-next-ripi-singh/